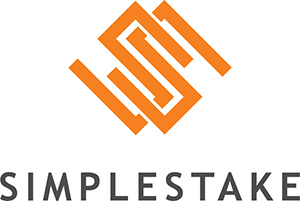
Impulse Staking
During the staking process, a solid or hollow “boss,” or tab, protruding through a mated part is heated to a softening temperature and formed to a head that captures the mated part.
Impulse Staking is a process that creates heat on-demand for staking plastic bosses of various sizes. The process is perfect for sensitive electronics and parts where excessive heat and pressure may cause damage to visible areas. At the end of each cycle, tips are cooled to room temperature within seconds preventing accidental operator injury and eliminating the need for constant heating – see our video below for an example.
Unlike heat staking and ultrasonic welding, Impulse Staking applies much less pressure on the part and provides a clean and string free method of staking. Impulse Staking is a proven process that once setup, requires little to no maintenance.
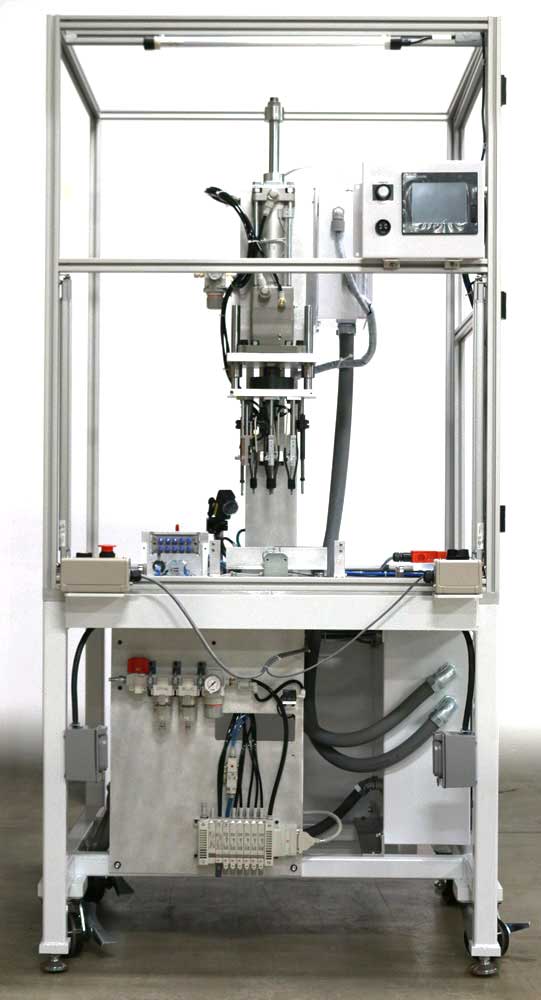
ToolTex Impulse Staking Machine
SimpleStake Handset 2
The same “heat on demand” technology of the Impulse Staking machine in a handheld, easy to use format. The SimpleStake Handset 2 is your solution for quick, efficient repairs or small scale jobs. This tool ensures a clean, string-free operation, remains cool post use, and the quick change tip system gives the flexibility of multiple handsets in one.
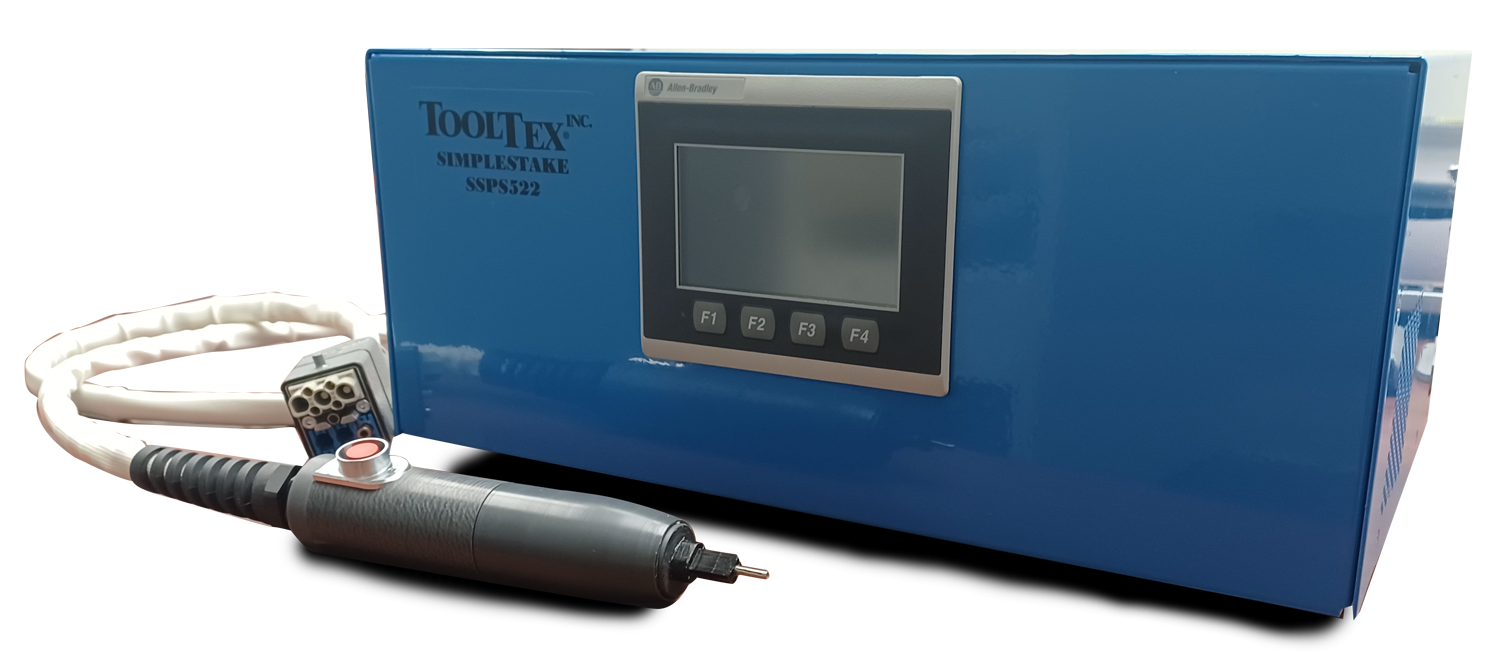
ToolTex SSH2 Impulse Staking Handset
Low Operating Costs, Low Maintenance & Easy Setup
SimpleStake is easy to set up as opposed to other methods of staking*. Operation costs are low with low to zero maintenance required.
No Stringing or Sticking
When compared to other methods of staking, SimpleStake’s Impulse Staking technology guarantees no stringing or sticking from happening.
Precision at its Finest & Total Process Cycle Control
SimpleStake can perform a less than 0.5” Center to Center precision which no other staking method can provide. Further, our technology gives operators total process cycle control.
Consistent Temperature & Clean Outcomes
Our Impulse Staking technology creates the ability to stake at a consistent temperature thus providing a clean and desired outcome.
HEAT
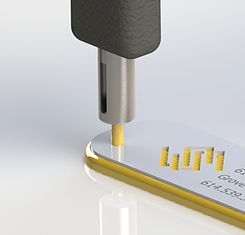
Parts are loaded into fixture, sensed for presence, and operator presses cycle start. Platen descends and all tips make contact with corresponding plastic "boss." Power is pulsed to the tip, creating heat at the boss/tip interface. This heat melts the boss and begins to form the button.
COOL
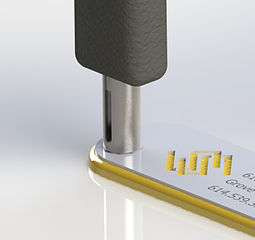
Once the heating cycle is complete and the tip is fully extended, a blast of compressed air enters the air tube and blows onto the back side of the tip, venting through the visible slots (see above). This allows the welded button to cool and form a strong bond with the mating part.
RELEASE
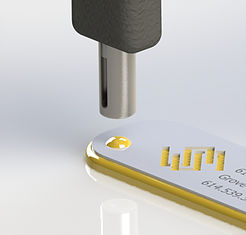
Now that the button is cool, a short pulse of power is applied to the tip in order to whet the surface of the plastic. This CleanRelease stage prevents sticking and stringing, common with other methods of staking. The welding is complete with a strong and lasting mechanical bond.