VIBRATION WELDING
Vibration welding produces a side-to-side scrubbing motion of low frequency energy, but it’s the high amplitude that creates frictional heat at the interface of the parts. Vibration welders are capable of very high pressures and have the ability to join very large components without the use of conventional adhesives or mechanical fasteners.
Need help with vibration welding applications? Contact Us for more information.
Applications
For very large or oddly shaped parts and engineered resins, often with high glass or filler content, Vibration Welding produces very high strength bonds that may not be achievable by any other means. The automotive industry utilizes vibration welding for under-hood components (intake manifolds, runners, duct assemblies), large “soft-touch” parts such as air-bag chutes and dash components as well as tail lamp assemblies and other exterior trim parts.
Precision
The scrubbing action stops at the same point it starts, maintaining mated part relationship, and vibration welders incorporate encoders to ensure desired closure geometry.
Joint Design & Tooling
As with all welding technologies, joint design is critical to integrity and appearance and special consideration must be given to tool weight, balance, clamping, adjustability and quick-change ability. ToolTex takes all of these factors into account to produce the most reliable and efficient tool, and currently have dozens of vibration weld tools in service today.
Processing
Often, there is no alternative to this process, but multiple part processing in a single cycle may be possible. Your mold cycle may determine if a multi-cavity tool can be beneficial to your application.

ToolTex TX120 Servo Vibration Welder
Read More >>
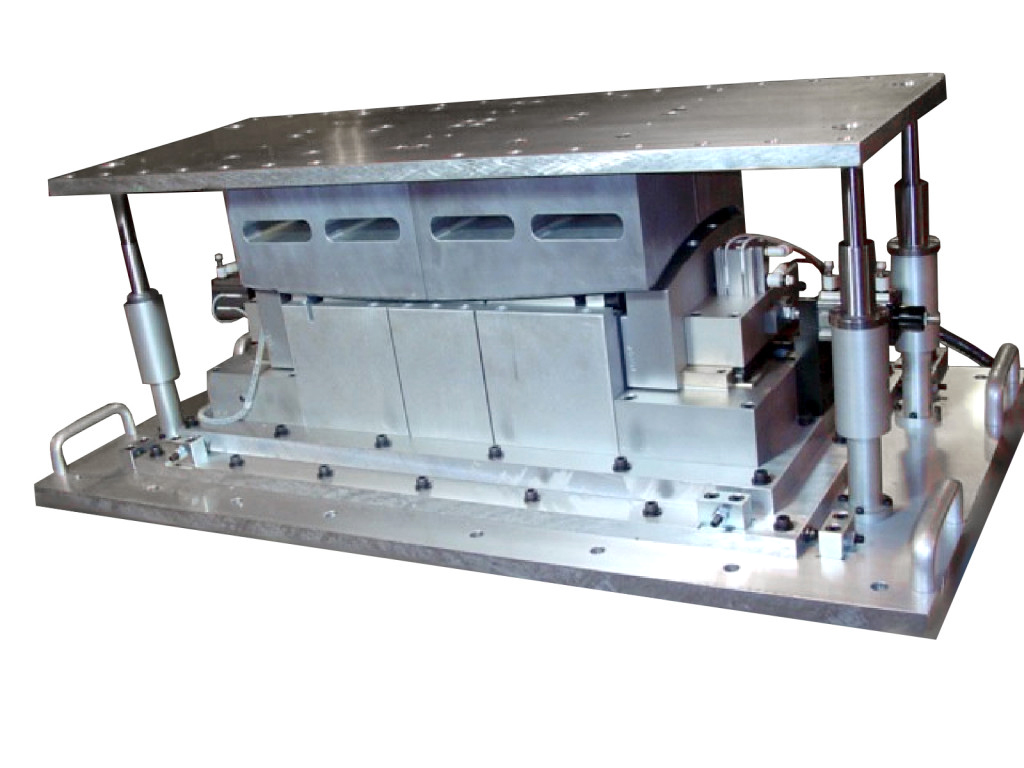
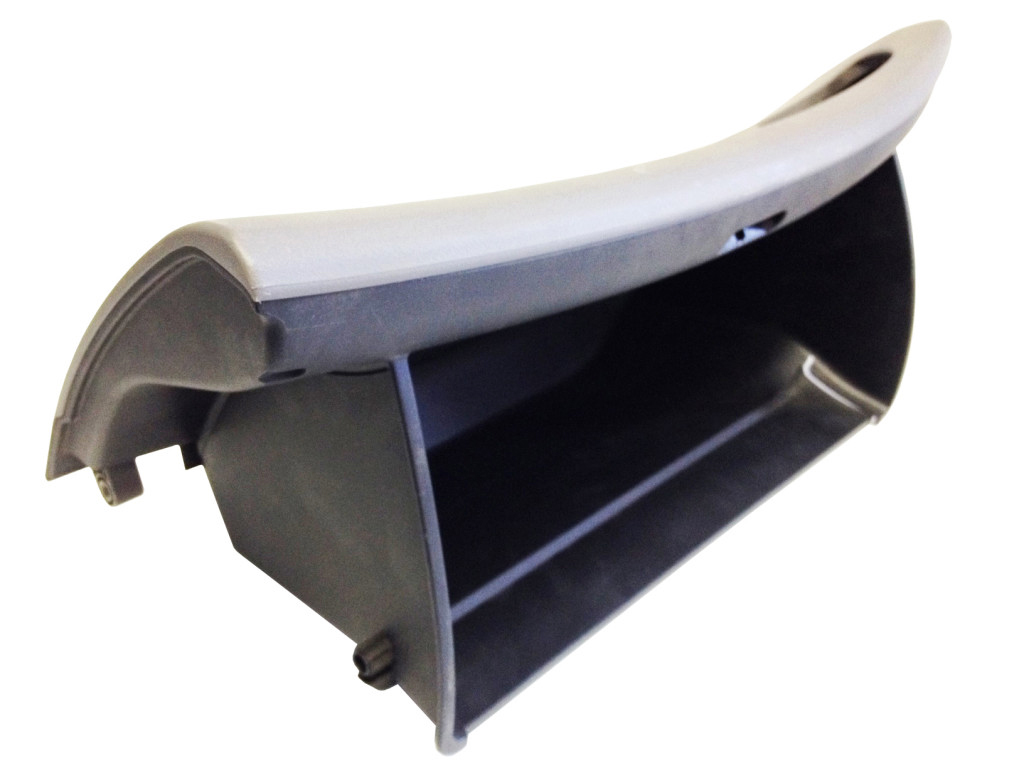